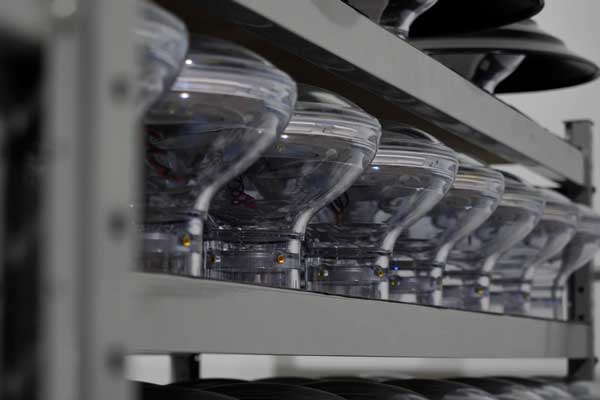
Moulded Material Grades
Solar Bollard Lighting® (SBL) uses only the patented SABIC LEXANTM SLX PC CO-POLYMER for our Dome Top cover due to the level of ultraviolet (UV) it must withstand during its operational life cycle.
Not all Polycarbonates have the same performance characteristics as explained further.
POLYCARBONATE (PC) IS MOST COMMONLY USED FOR SOLAR BOLLARD LIGHTS DUE TO ITSPOLYCARBONATE (PC) IS MOST COMMONLY USED FOR SOLAR BOLLARD LIGHTS DUE TO ITS
Polycarbonate grades will perform differently when exposed to ultraviolet (UV):
STANDARD HIGH IMPACT POLYMER WITH A UV ADDITIVE – MOST COMMONLY USED
SABIC LEXANTM SLX PC CO-POLYMER – ONLY USED BY SBL
Sabic LEXANTM SLX co-polymer vs high impact polymer with UV additive.
6 YEARS SIMULATED WEATHERING
– UV oxidisation effect
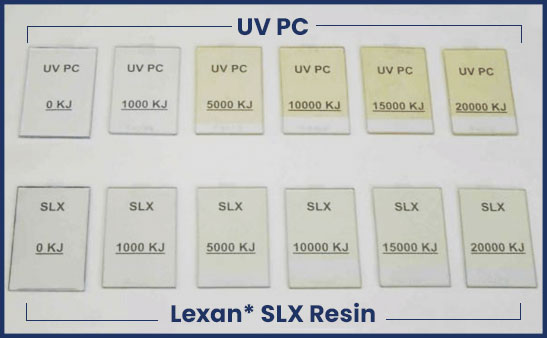
3 YEARS SIMULATED WEATHERING
– UV oxidisation effect
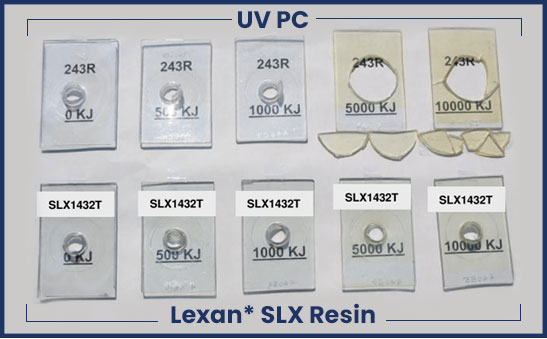
HIGH IMPACT PC – ALMOST UNBREAKABLE
Impact protection (IK10) testing of SBL2 Series Solar Bollard Light to AS/NZS60529:2004 and IEC62262:2002. Real-life testing shows impact resistance from repeated strikes from a 3kg (6.6lb) sledgehammer.

ACRYLIC (PMMA)
NYLON (PA)
MOULDING CAPABILITIES USED BY SBL
Injection moulding can make a big difference to the finish quality of the moulded components and the product’s the long-term reliability:
The following examples are of high impact PC polymer with a UV additive which is an easier material to mould and therefore weakens the actual part:
MOULDING IMPERFECTION OF LOW-GRADE COMPETITOR PRODUCTS
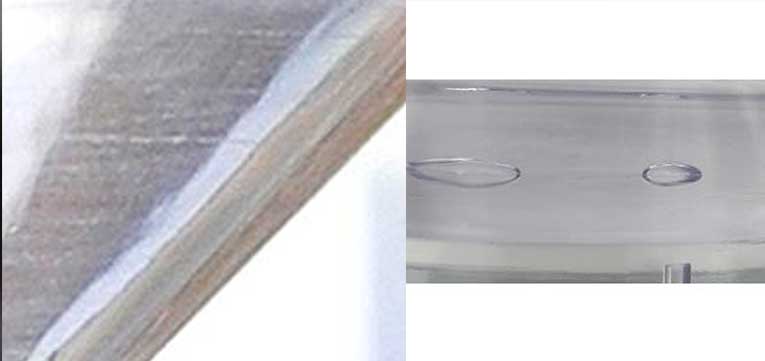